Production development and process analysis

Delfoi Consulting acts as the customer’s partner in demanding production development and productivity improvement projects and change programs.
Even in the most demanding improvement programs, the goals can be achieved by combining the customer’s data and personnel’s knowledge of production and logistics processes with Delfoi’s methods and experience in using them in hundreds of successful projects. In the initial stages of a comprehensive development program, the goals are specified in greater detail and typically include:
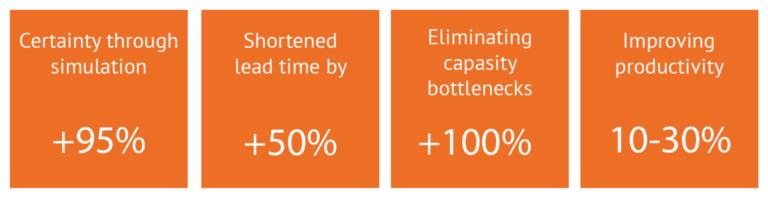
Delfoi has carried out productivity improvement projects since 1990. Our ability to improve the productivity of our customers is based on experience accumulated from hundreds of customer projects over three decades as well as our solid background in simulation.
Regardless of the industry or the initial situation, waste in different forms, is always present at operations processes. Luckily, it can be eliminated. Boosting productivity or increasing capacity does not automatically require implementing some new production philosophy or investing in new equipment or facilities. Delfoi Consulting designs and validates a specific production development solution for its customer, based on the actual current situation and objectives. Identifying waste is the starting point for successful development, and various bottlenecks in production and logistics can be eliminated by first optimizing the processes and then planning and controlling the process by exact data.
Customer reference stories
The current state analysis of processes helps locate the most impactful development actions and creates a numeric benchmark for measuring the improvement
Understanding the current state of production is as important as knowing your location in orienteering; if you don’t know where you are, it’s extremely difficult to navigate to a given destination!
The process development needs and opportunities established by the current state analysis are summarized into an overall process mapping that can be used to calculate the potential for development and a point of reference for improvements. Varying the production volumes and mix helps to analyze bottle-necks and explains the behavior of outputs such as warehouse levels, use of capacity and lead times. After the overall process mapping is done, a more detailed examination of various processes follows, and the right sub-processes are selected for a thorough process analysis. Methods used in the thorough analysis include observation and process walks, value stream mapping and process descriptions, bottleneck analysis, segmentation models, cause-effect analyses and more detailed statistical modeling of time usage and process waste. Process descriptions of the current activities can also be documented for later use, during the work.
The result of the analysis depicts the current state of production and the most impactful development actions in the entire process. In the later stages of the development, more detailed current state analyses can be carried out, but it is important to establish an overall process mapping first.
- Cycle time analysis and the share of value-added / non-value-added time
- Material flow analysis of the plant, warehouse, or logistics center
- Capacity utilization analysis (key equipment, personnel, facilities)
- List of targets for development and preliminary estimate on improvement potential
Solution design and validation
After the current state analysis, production development process moves on to designing and validating the solutions. At its easiest, this could mean solving a single bottleneck in production. However, large-scale production and logistics systems usually require the simultaneous development of several processes and factors, especially when aiming for radical changes in productivity or capacity. For example, the planning and deployment of a new plant or logistics center should always be viewed as a comprehensive change project where achieving the benefits requires parallel development of the processes, facilities, and production control. A new plant designed around an old process is not the most optimal way of investing in plants; starting with a clean slate is usually the best approach.
The development workshops facilitated by the experts of Delfoi Consulting are designed for process-driven development and create the foundation for one or more design options. The development workshops in the initial stage include a planning workshop for the ideal situation of one overall process as well as the necessary number of workshops for more specific development targets (such as layout, production management, manufacturing processes or internal logistics) and one workshop for prioritizing and outlining the options. Simulation modeling of production or logistics is used for validating extensive development needs, and the assumptions and initial data required for the simulation are specified in the workshops. A wide range of executives and experts take part in the planning-stage workshops.
Learn more about the use of simulation.
Once the impact of the options has been sufficiently analyzed, the proposed solution is presented to the company’s decision-makers and the necessary choices are made to proceed into implementation. After decision-making, the more detailed planning and implementation moves forward as a cooperation between the customer and the other parties involved in the implementation, depending on the chosen solution. The implementation and deployment of the chosen solution can happen almost instantly for quick development targets. An extensive implementation can take years if the target is the deployment of a new facility or the rearrangement of a supply network. During the implementation stage, the customer’s process can be supported by means of change management consultancy and process evaluations from Delfoi. Modeling and simulation help respond to external changes along the way, allowing corrections to the plan, if needed. Once the new production process is up and running, it is extremely important to also plan and control it in an efficient manner and to use modern and efficient tools in the production planning. Delfoi Planner solution can be implemented for a continuous operation use phase.
Learn more about the Delfoi Planner solution